Load Handling Device Options For Workstation Cranes Enhance Ergonomics
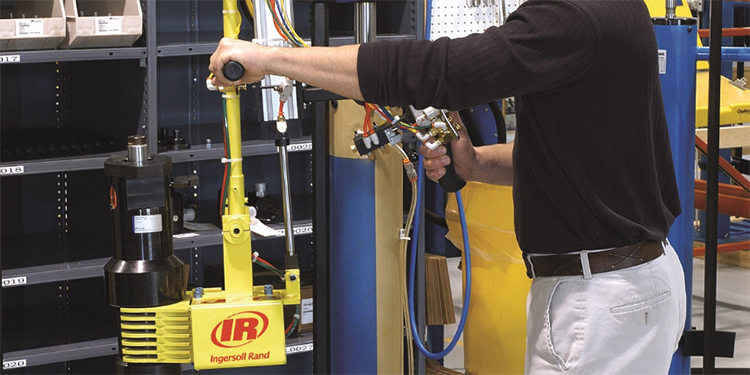
When assisted by workstation cranes installed overhead in manufacturing and assembly work cells, operators can lift, lower, handle, position, and move heavy objects safely and efficiently. As it serves as the connection between the workpiece and the crane’s hoist and trolley, choosing the optimal ergonomic handling device is critical. This ensures that the system operates properly while maximizing operator ergonomics by minimizing the risk of overexertion, fatigue, repetitive stress, and injury. For that reason, ergonomic handling devices may be specified in a variety of standard and customized designs, operational functions, and capacities.
When selecting an ergonomic handling device, it’s important to work with a manufacturer or supplier to ensure the optimal solution is deployed. To determine what type or style of handling device is best suited to a process, the best practice is to work with an ergonomic handling/lifting company to understand and assess the task required. Some processes only require the operator to pick up a load at point A then transfer it to point B. Others involve more complicated movements, such as rotating the part to a certain angle, flipping it over, and inserting it into a piece of machinery. Having a solid understanding of the required process helps the load handling device engineer to make recommendations about the style and functionality that will perform most efficiently while requiring the least amount of ergonomic effort from the operator.
Further, the engineer will evaluate the specifications and characteristics of the part itself: shape, size, weight, construction, material, finish, balance, center of gravity and more. This ensures that the load will be handled safely and properly by the device without causing damage.
There are a variety of common lift assist devices available. Depending on the application and the load to be handled, each of these styles can be customized as needed to best suit the process. The primary styles include:
- Grippers or clamps: Incorporating flat or curved tongs or clamps, these devices use friction or pressure to grip the load via clamping action.
- Magnets: Specifically used with ferrous items, these devices may or may not include an electrical power supply to charge the magnet as it lifts, carries and releases the load.
- Vacuum lifters: Equipped with vacuum pads or cups, when activated by the operator these attachments create a vacuum that connects and secures the device to the load.
- Probes: Used to lift coils or rolls of material, these devices are inserted into the central core of the load to lift it from inside so as not to damage the product.
- Hooks: A C-shaped connection that latches on to the load either directly or via a sling, strap or chain.
Additionally, because ergonomic handling devices can be attached and detached from the hoist, they allow an operation to modify a workstation crane for use with another device to handle a different load (providing that the second load falls within the overall rated capacity of the crane). This interchangeability can extend the life of the initial workstation crane investment while further ensuring proper operator ergonomics, regardless of the load or task.
Want to learn more about workstation cranes and how they can help your operators be both safer and more productive? The members of the Monorail Manufacturers Association (MMA) are the industry’s leading suppliers of workstation crane systems. The group offers a variety of resources—including a product certification program, recommended practices for workstation cranes and patented track systems, and more—via its website at www.MHI.org/MMA.