Webinar Explores Best Practices In The Safe Operation Of Below-The-Hook Lifting Equipment
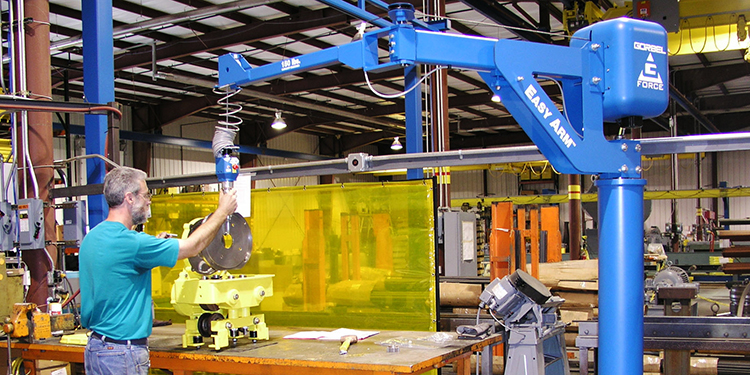
The last of four sessions featured in the fourth annual Overhead Lifting Safety Webinar Series (www.mhi.org/overheadsafety), “Best Practices for Safe Operation of Below-the-Hook Lifting Equipment,” aired on November 18. During the hour-long presentation, Scott Salisbury, General Manager at Bradley Lifting Corp., shared an in-depth review of best practices for the proper use of below-the-hook lifting equipment. He also discussed how training, maintenance, and inspection of this equipment ensures maximum safety and service life.
At the outset of the session, Salisbury provided a brief visual overview of the most common types of below-the-hook lifting equipment, defining it as any device used for attaching a load to a hoist (such as C-hooks, sling hooks, strap hoists, pallet lifters, magnets, lifting beams, grippers, drum turners, vacuum lifters, sheet lifters and more). Regardless of the type of device being utilized in an application, there are certain key guidelines for their safe operation that are universal, he said.
The primary safety standard for the operation and use of below-the-hook lifting devices is ASME B30.20, published by The American Society of Mechanical Engineers. It includes provisions for the marking, construction, installation, inspection, testing, maintenance, and operation of below-the-hook lifting devices used for attaching loads to a hoist. Its contents apply to structural and mechanical lifting devices, vacuum lifting devices, magnets, grapples, and clamps used for positioning and anchoring. Salisbury added that different ASME standards apply to other below-the-hook devices: ASME B30.9 applies to slings, ASME B30.10 applies to hooks, and ASME B30.26 applies to rigging hardware.
He also advised owners and operators reference the recently released Operator’s Manual published by the Crane Manufacturers Association of America (CMAA) specific to the use of below-the-hook lifting devices.
Among the key points regarding safe operation of these devices are to:
- Ensure that only qualified personnel operate below-the-hook equipment,
- Train personnel specifically on the proper use and operation of each below-the-hook device,
- Only permit trainees to operate the equipment under the supervision of a qualified staffer, and
- Anyone charged with training others, maintaining, or inspecting the device should be qualified to do so.
Further, continued Salisbury, if the operator has any concerns about the safety of the lifting device, they should place the load in a safe position and cease the equipment’s function until all potential issues have been addressed.
Other important safe operation best practices include:
- Not allowing an operator who has not read the manual for the device to use the equipment.
- Loads that exceed the rated capacity of the lifter should not be handled by the equipment.
- The lifter should not be used for any other purposes than that for which it has been designed, including lifting people.
- Damaged or malfunctioning equipment or equipment missing parts or safety/warning labels should not be used.
With regard to inspections, Salisbury emphasized the impact usage, load weight, and environment on the degree of service frequency for the equipment. He defined service qualifications with information about normal, heavy, severe, or special/infrequent classifications. Keeping records of findings noted during lift, periodic, and frequent inspections is strongly recommended, and any deficiencies should be examined by a designated (and qualified) individual to determine if they constitute a hazard or necessitate additional inspections. Salisbury shared visual examples of several types of deformations, damage, and wear, as well as of missing guards, rigging issues, cracked or bowed latches, damaged electrical components and motors, and more.
To conclude the presentation, Salisbury discussed the importance of repairs being performed properly in order to ensure the safety of the equipment. Best practice is to consult with the equipment’s original equipment manufacturer (OEM) regarding approved repair procedures and replacement parts. He also emphasized the impact of a repair on load testing. The same best practices apply to any modifications that may be performed on the equipment post-installation, he added.
The Overhead Lifting Safety Webinar Series is presented by MHI’s Overhead Alliance, which includes the Crane Manufacturers Association of America (CMAA), the Hoist Manufacturers Institute (HMI), and the Monorail Manufacturers Association (MMA). Designed for owners, operators, maintenance, and safety personnel responsible for overhead lifting cranes and hoists, the series features presentations and Q&A from several industry experts and a representative from the Occupational Safety and Health Administration (OSHA). The other three topics covered include:
- Dangers From Above: Integrating Overhead Lifting into a Resilient Safety Strategy
- OSHA Overhead Lifting Safety Review and Presentation of Upcoming Initiatives
- Overhead Lifting Safety Innovations and Panel Discussion
It’s not too late to gain access to the webinars. All four presentations have been recorded and are available with paid registration of $300, which also includes complimentary copies of safety and specification publications from the Overhead Alliance (a $260 value).
To register to view the Overhead Alliance’s Overhead Lifting Safety Webinar Series, visit www.mhi.org/overheadsafety.